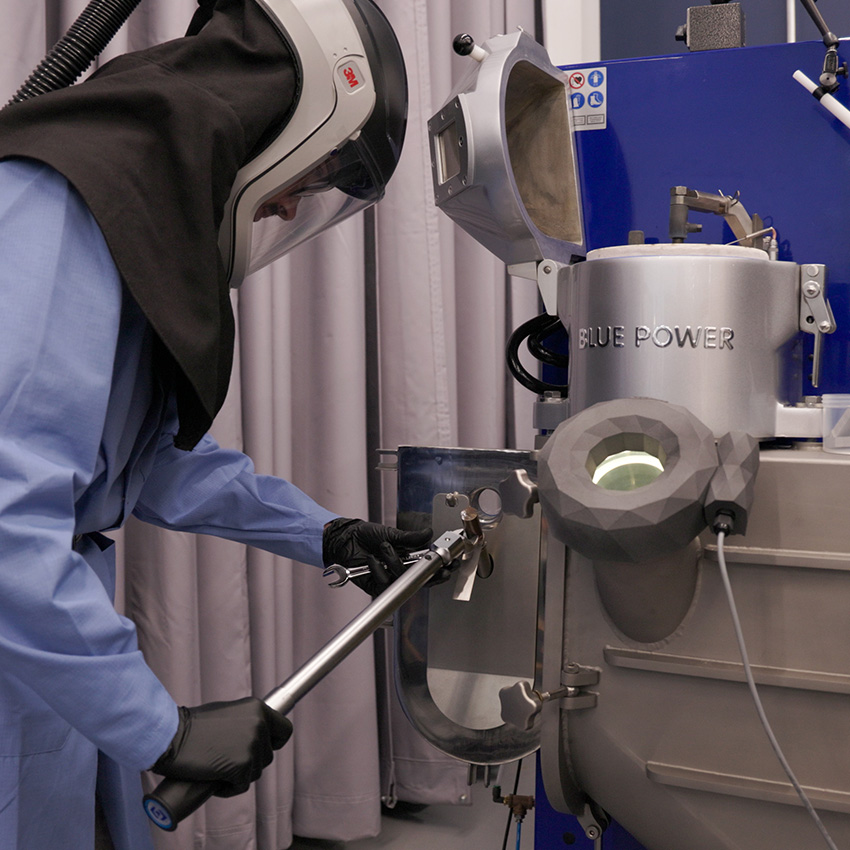
Materials and Advanced Material Development
GTMI advances global manufacturing by developing innovative materials and cutting-edge techniques that enhance strength, reduce weight, and increase versatility. Our research in composites, metals, polymers, and ceramics drives more efficient, sustainable, and high-performance production.
Advanced Material Development Research
Materials generation and production serve as the launch-point for delivering scientific breakthroughs to industry. Unlike traditional methods that often follow established processing steps, many newly developed materials require entirely new methods for production at both research and industrial scales. GTMI is making significant investments in physical production capabilities to facilitate the industrial adoption of new materials and enhance the production techniques for already common materials.
GTMI's approach to materials generation includes the development of new powder production techniques, additive manufacturing, and modeling of novel deformation processing. These advanced methods enable the creation of materials with unique properties and improved performance, driving innovation and efficiency in manufacturing processes. By integrating these cutting-edge techniques, GTMI ensures that new materials can be produced cost-effectively and at scale, bridging the gap between research and real-world application.
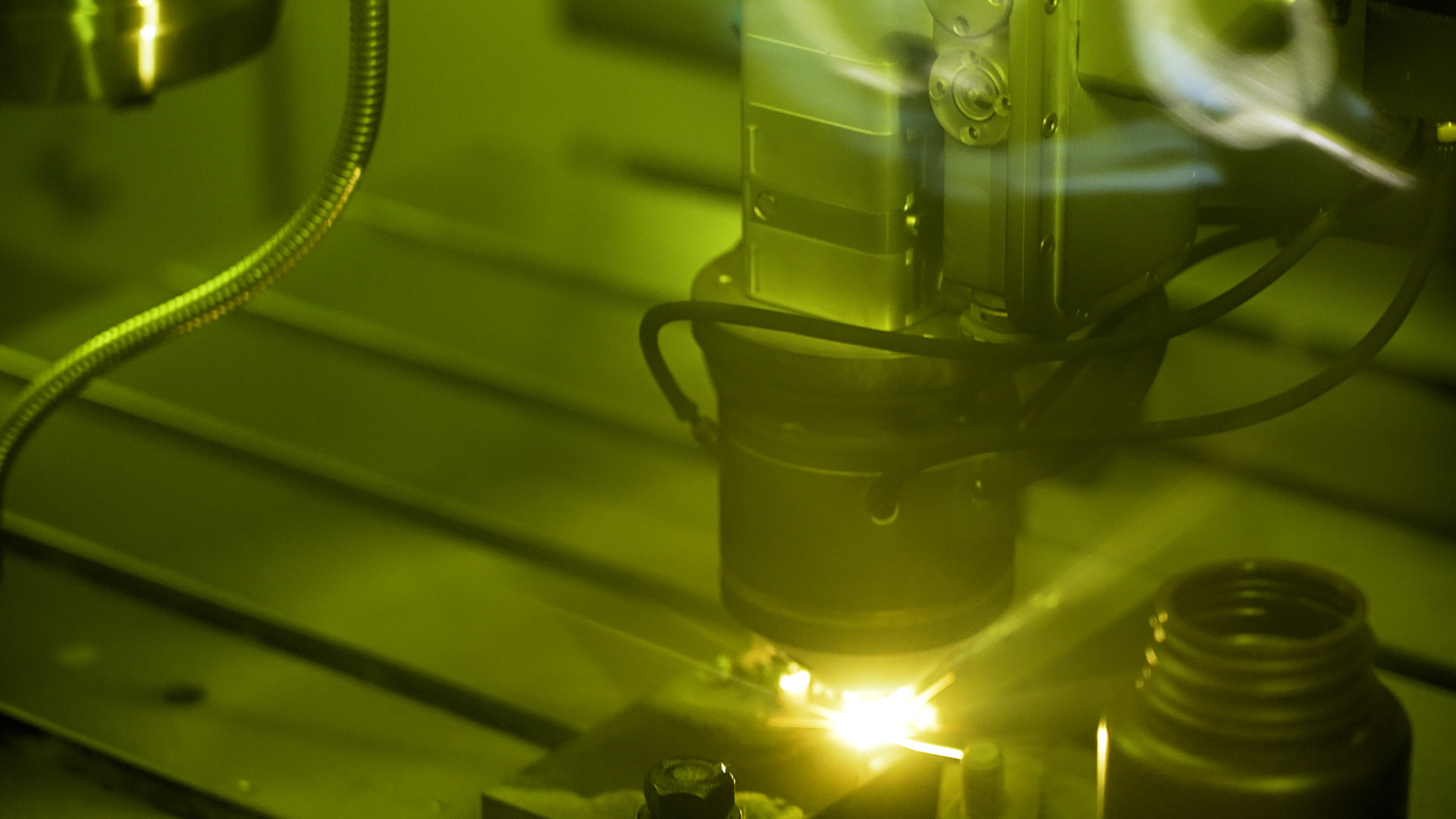
Metals
Metallurgy is a cornerstone of high-strength, high-performance materials. At GTMI, our work in metals focuses on innovative projects that push the boundaries of material science and engineering. We are dedicated to advancing the production and application of metals through cutting-edge research and development.
Our projects include in-house metal powder production of high-temperature alloys for 3D printing rockets, leveraging density functional theory (quantum mechanics-based software) to predict new alloy properties, and additive manufacturing of high-temperature alloys, aluminums, and steels. We also specialize in the additive manufacturing of graded components, where parts are made of two different metals that gradually transition between each other, and the development of shape memory alloys that change shape when heated.
Additionally, we conduct thermodynamic-driven simulations to determine the suitability of metallic alloys for use in additive manufacturing. These efforts ensure that we remain at the forefront of metallurgical innovation, providing high-performance materials that meet the demanding requirements of modern industries.
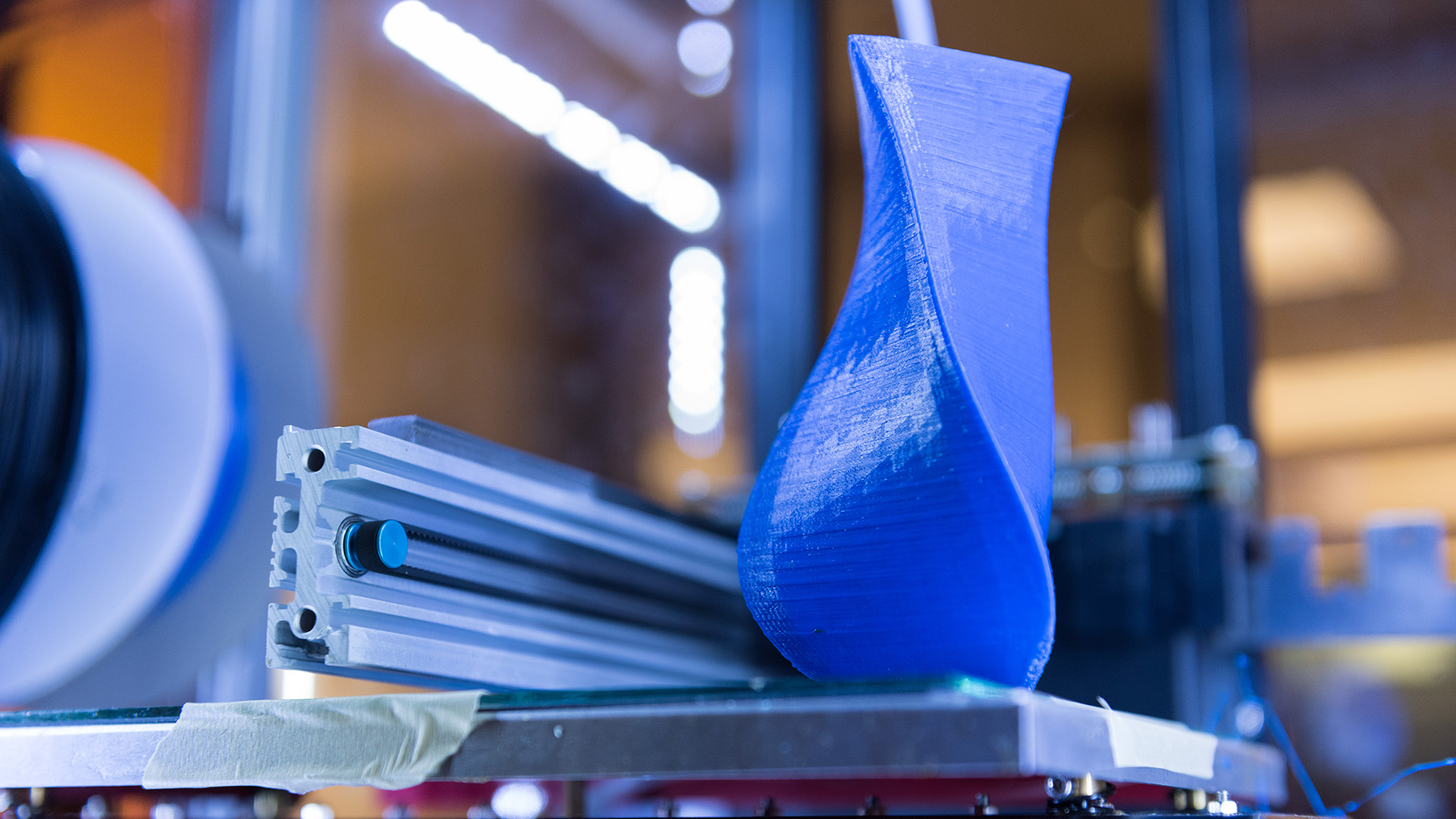
Polymers
Polymers are essential for a wide range of applications due to their versatility, durability, and adaptability. At GTMI, our work in polymers focuses on innovative projects that enhance the properties and applications of these materials. We are dedicated to advancing polymer technologies through cutting-edge research and development.
Our projects include the development of advanced polymer composites, which combine polymers with other materials to improve their mechanical, thermal, and electrical properties. We also focus on the additive manufacturing of polymers, enabling the creation of complex and customized components with high precision. Additionally, we employ techniques for the characterization and testing of polymers to ensure their quality and performance in various applications.
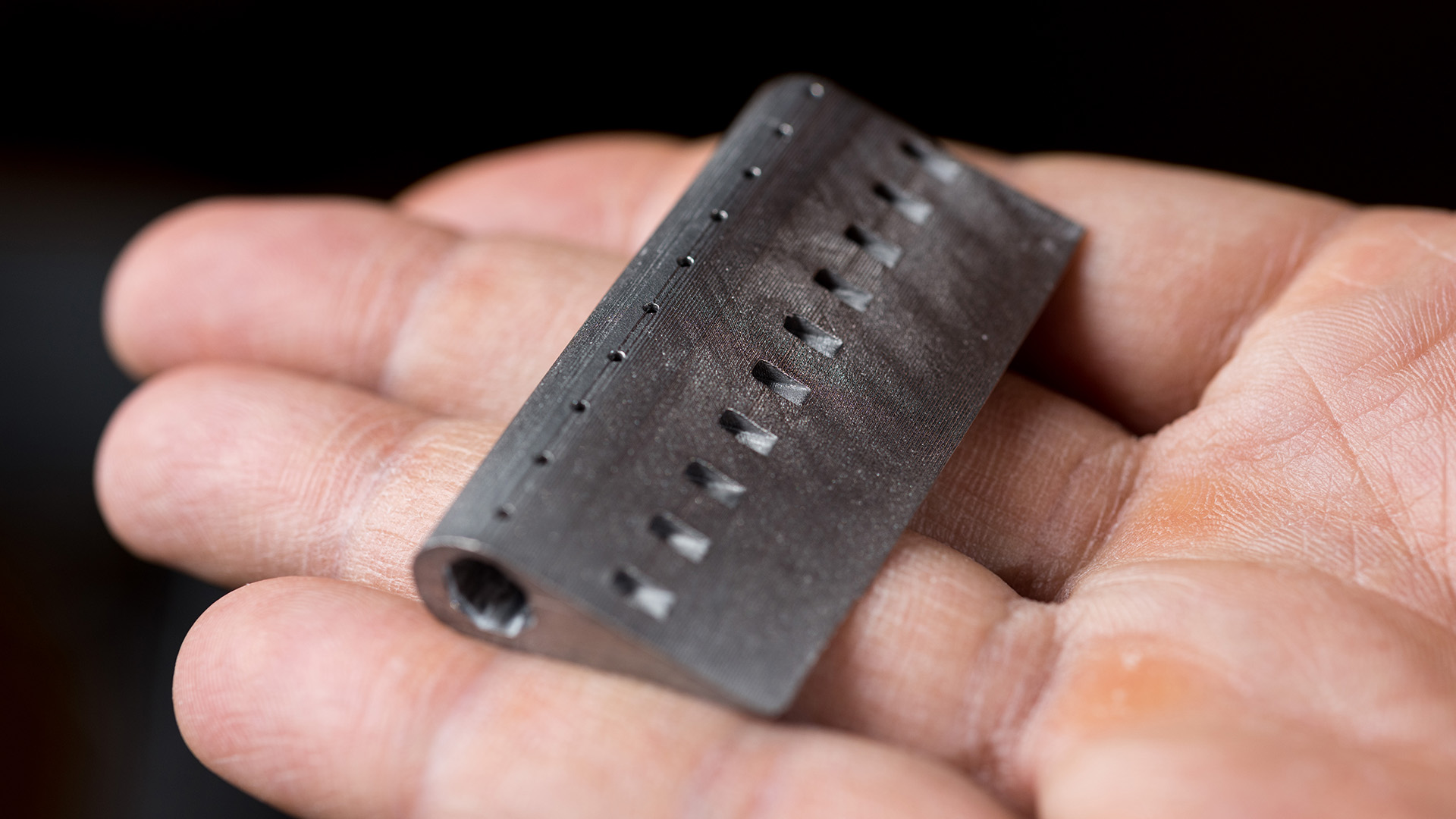
Ceramics
Ceramics fulfill many unique load-bearing, electronic, and thermal needs. At GTMI, our work in ceramics focuses on innovative projects that enhance the properties and applications of these versatile materials. We are dedicated to advancing ceramic technologies through cutting-edge research and development.
Our projects include the development of metal matrix composites, which incorporate large volumes of ceramics within metals to improve their properties. We have several experts working on additive manufacturing of these composites, ensuring that they meet high-performance standards. Additionally, we employ non-destructive techniques such as ultrasonic testing and screening of ceramic components to detect defects. This approach reduces wasted time working with parts that may fail or not pass quality inspection, ensuring higher quality and reliability.
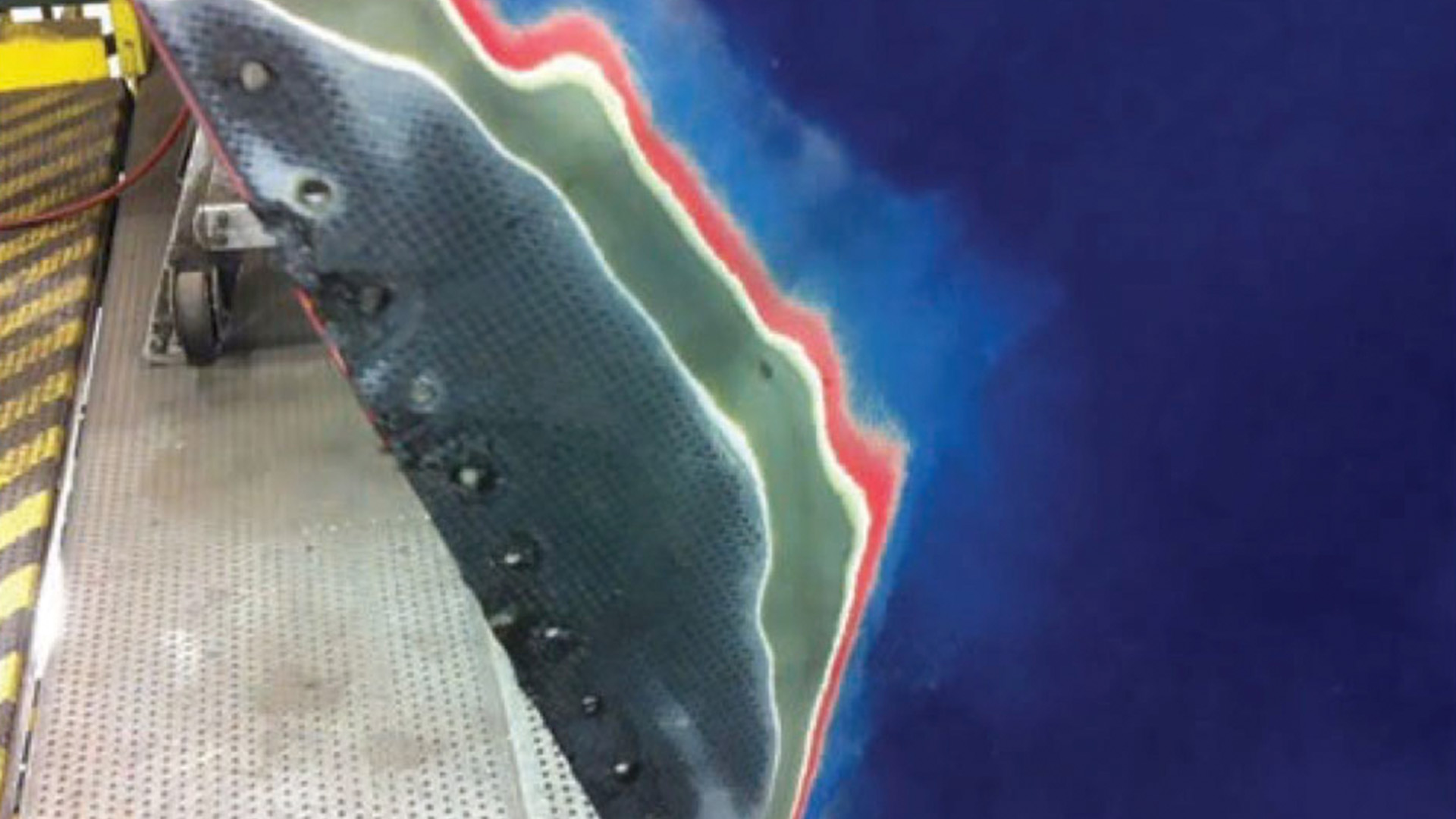
Composites
The composites industry significantly contributes to the U.S. economy, adding over $20 billion annually and projected to reach a global market value exceeding $180 billion by 2028. Composites are increasingly used in aerospace, automotive, infrastructure, biomedical, and sporting goods due to their lightweight, design flexibility, and corrosion resistance. GTMI develops innovative technologies for these sectors, leveraging interdisciplinary research and partnerships to advance from early-stage research to industry-ready solutions. Representative projects include developing composite materials for hypersonic vehicles (DARPA), scalable nanocellulose composites for automotive applications (Hyundai America), innovative 3D printing and materials development processes (Solvay-Cytec, now Syensqo), non-destructive inspection techniques (Lockheed Martin), and accelerated process development optimization and materials testing with machine learning (Delta Air Lines). GTMI’s comprehensive facilities, such as the Digital Composite Joining and Repair Lab, support this cutting-edge research.
Center for Composite and Hybrid Materials Manufacturing
The Center for Composite and Hybrid Materials Interfacing (CHMI) aims to revolutionize the joining and repair of composite and hybrid structures. As one of the NSF Industry/University Cooperative Research Centers (IUCRCs) at Georgia Tech, CHMI is funded for five years and collaborates with leading manufacturers and government organizations. Located within the Georgia Tech Manufacturing Institute (GTMI), CHMI includes research teams from Georgia Tech (aerospace thrust area), Oakland University (automotive thrust area), and the University of Tennessee, Knoxville (infrastructure and medical devices thrust areas).