
From Lab to Market
At the Georgia Tech Manufacturing Institute (GTMI), we’re committed to transforming and scaling world-class research into real-world applications and value for our external partners. Since our inception in 1991, we’ve collaborated closely with industry, government, national labs, and leading academic institutions to position the manufacturing industry for the future.
Synergistic Results
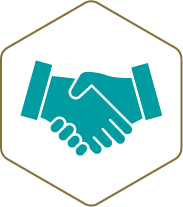
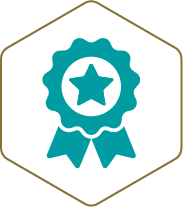
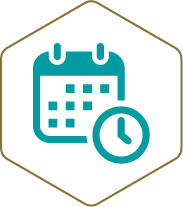
Partnered Initiatives
Advanced Manufacturing Pilot Facility (AMPF)
As a flagship component of GTMI, the Advanced Manufacturing Pilot Facility (AMPF) is a special place where industry works alongside researchers and students to take early-stage concepts from idea to reality. Initially funded by a generous gift from the Delta Airlines Foundation, this 20,000 square foot and growing, reconfigurable user facility serves as a state-of-the-art technology testbed for manufacturing innovations, as well as a teaching facility for our stakeholders.
For information on engaging in a similar partnered initiative, contact Belinda Vogel.
Manufacturing 4.0 Consortium
GTMI’s Manufacturing 4.0 Consortium is a member program focused on adding value to our industry partners, helping companies of all sizes to become global leaders in industry 4.0 solutions. Through the Consortium’s workshops, trainings, and quarterly meetings, GTMI and member companies are mapping the path to positive ROI and workforce development using 4.0 technology and practices.
For more information about the Consortium, contact Steven Ferguson.
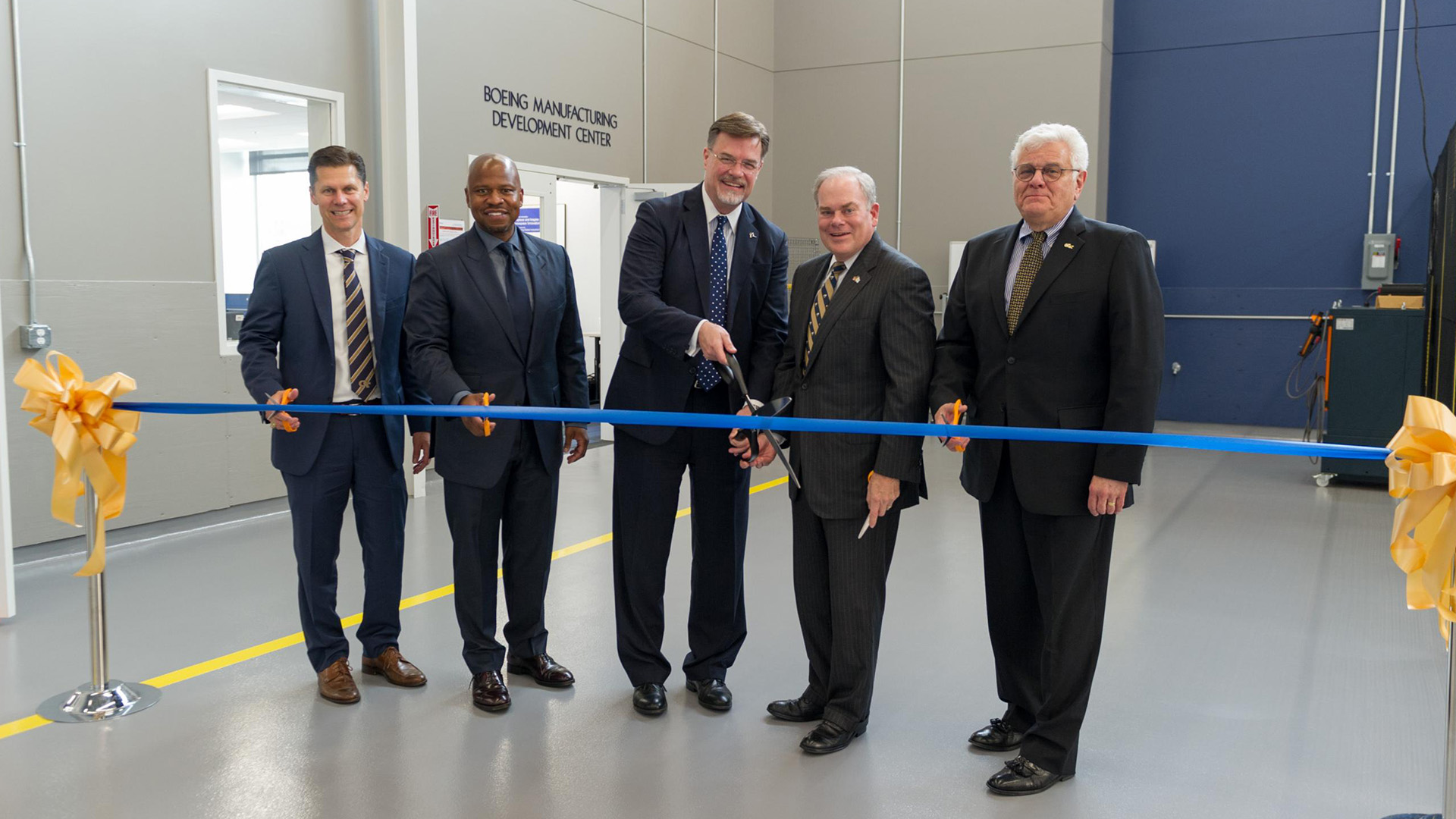
Boeing Manufacturing Development Center
Housed in AMPF, this Boeing research laboratory works to tackle important technical challenges in robotics for manufacturing and aerospace assembly applications. Researchers from Boeing and Georgia Tech work side by side, implementing automation solutions for industrial applications.
For more information about the Boeing Manufacturing Development Center, contact Shreyes Melkote.
Industry Directed Research Projects
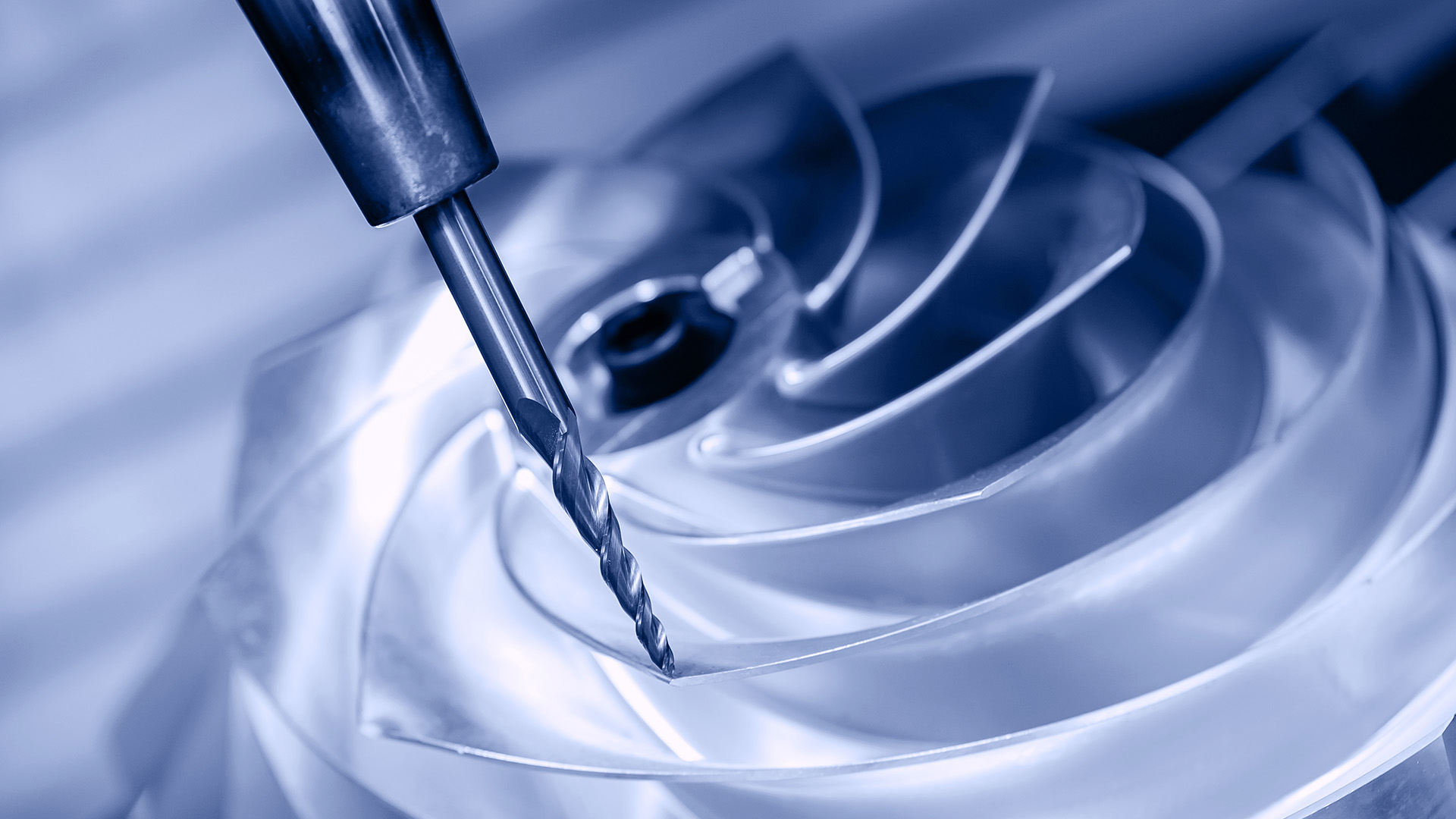
Tracking Persistent IDs for Traceability
Graduate students at Georgia Tech are collaborating with a major manufacturer to improve the traceability of machining toolpaths. The project began with a proof of concept, demonstrating how to assign unique, persistent IDs to these toolpaths. Now, the team is working on automating this process and determining which Product Manufacturing Information (PMI) annotations require persistent IDs due to their impact on the final product's characteristics.
By implementing traceable, persistent IDs, the manufacturer can pinpoint issues in the production process at any stage of the product's lifecycle. This innovative approach has the potential to become an industry standard, offering manufacturers greater precision and insight into their operations.
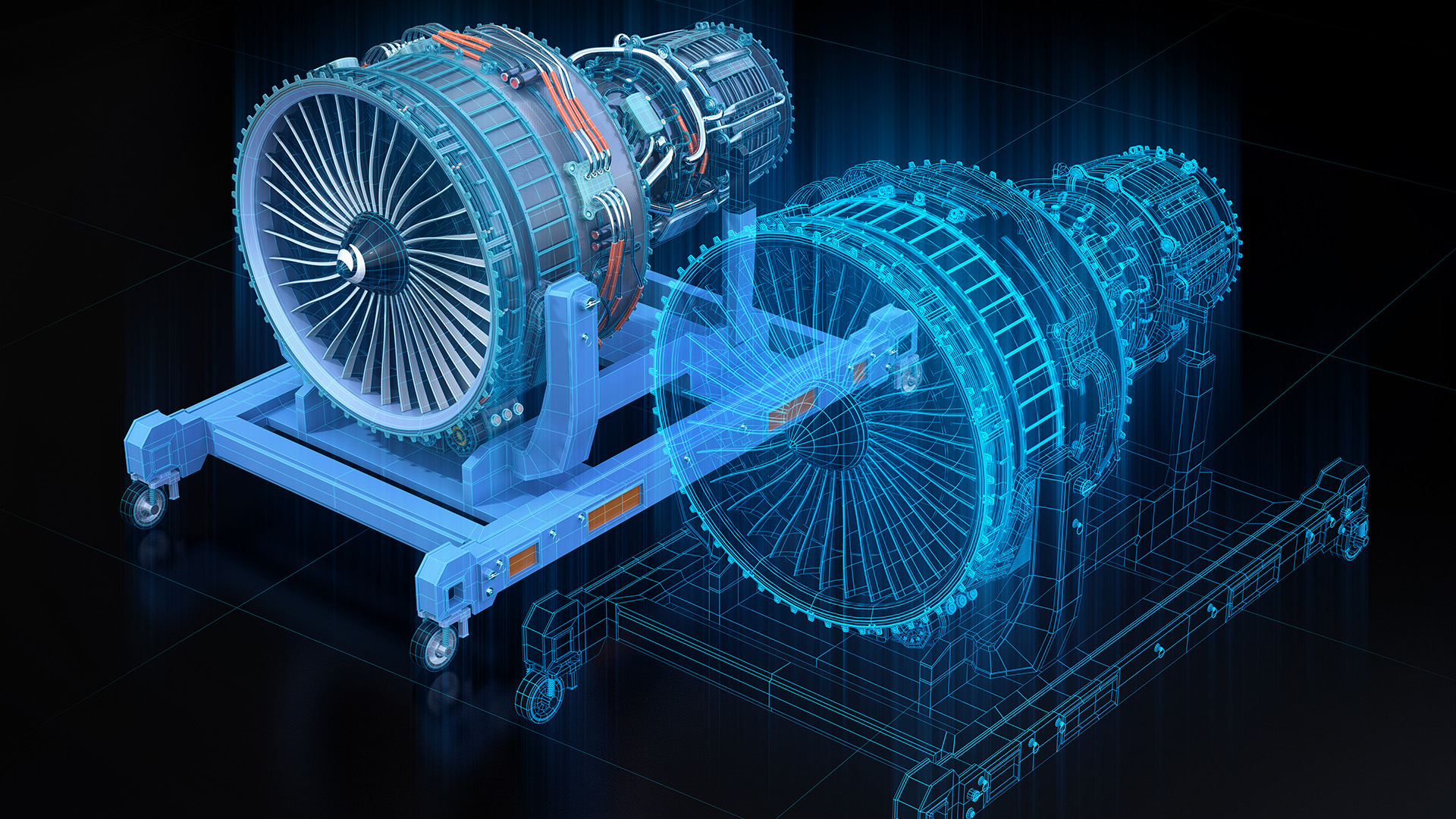
Advancing Digital Twin Capabilities
At GTMI’s Advanced Manufacturing Pilot Facility (AMPF), our collaboration with machine tool producers, robotics companies, and software providers is enhancing digital twin capabilities. With contributions from three industry partners, GTMI is setting up a system to resurface build plates, integrating a machining platform, a donated robot, and control software.
This setup automates lab processes and develops digital twin scenarios. The robot can also switch tasks, like polymer printing, while waiting for machining to finish. This collaborative effort not only advances research but also provides valuable feedback to the participating companies.
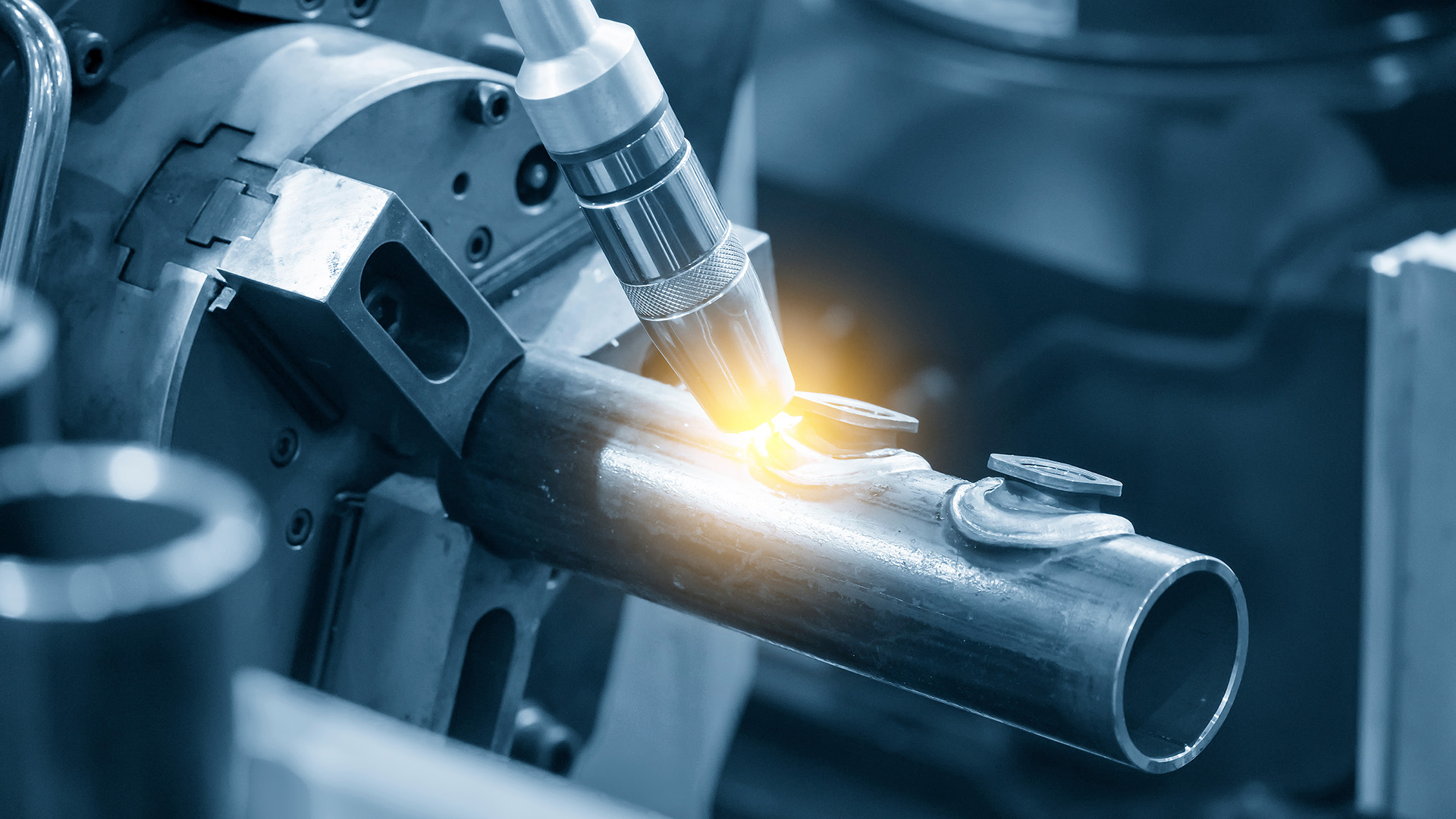
Additive Repair
Through America Makes, GTMI helps U.S. manufacturers repair parts using an additive and subtractive process. These parts are refurbished to meet specifications, often with harder materials for better durability. For instance, a cylindrical part used in manufacturing was successfully repaired and returned to service.
The process involves probing parts to understand wear patterns, developing tool path strategies for machining, depositing new material, and final machining to the desired geometry. Post-repair inspections ensure the parts meet design specifications. Repairing these parts costs less than 30% of buying new ones, potentially reducing costs and waste for companies that use thousands of these parts annually.
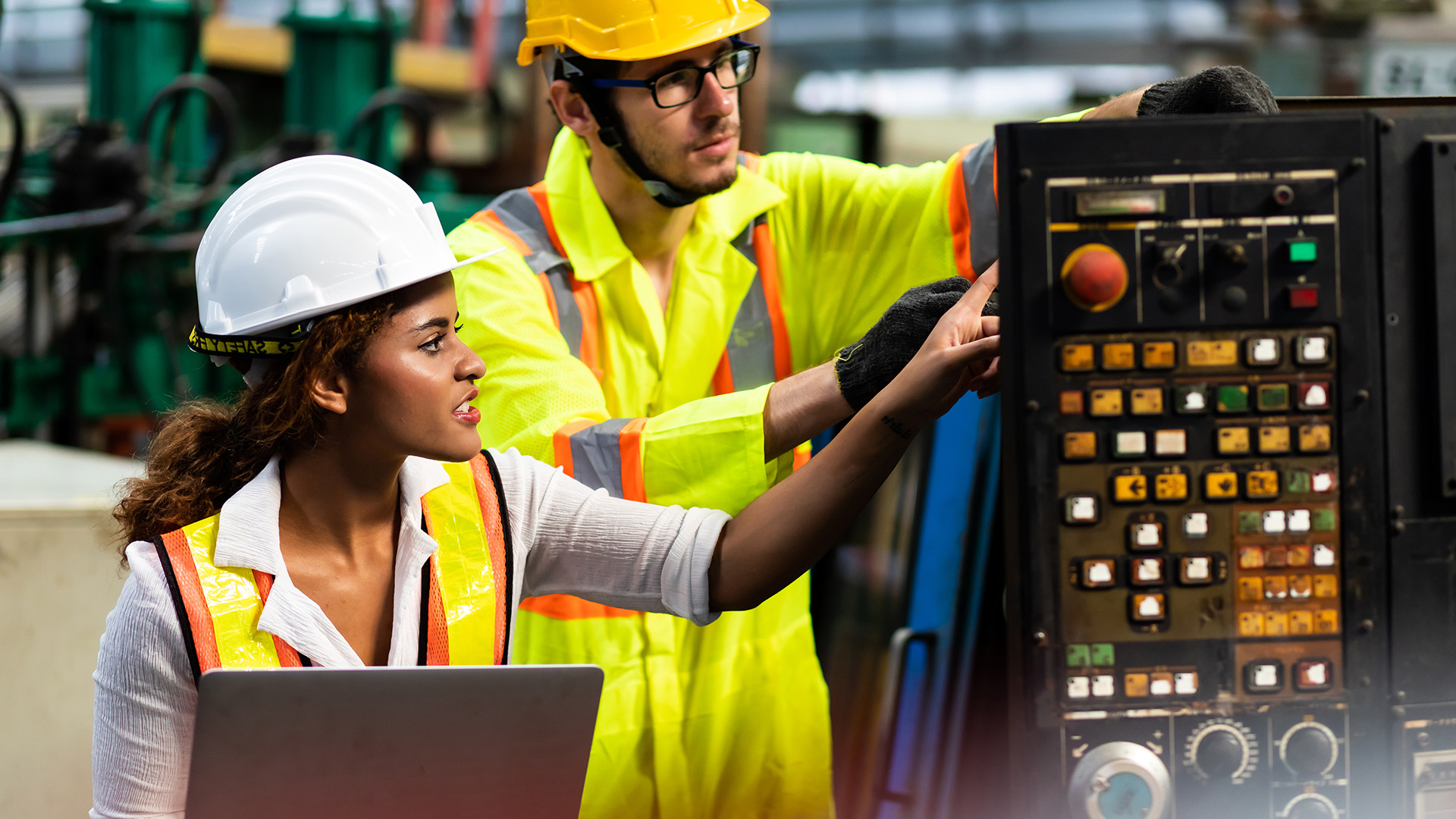
Data-driven Manufacturing Capability Modeling for Resilient Cyber Manufacturing
Traditionally, understanding the capabilities of manufacturing processes and equipment has relied on human experience, which is hard to scale. Rule-based methods have also proven inadequate in accurately describing the true capabilities in terms of shapes, materials, and quality characteristics.
Georgia Tech faculty and students, in collaboration with industry researchers from a major manufacturing company and supported by an NSF Future Manufacturing Research Grant, are developing AI/ML methods to infer manufacturing process capabilities. These methods aim to automate gaps between design and manufacturing, enhancing the resilience of the industrial manufacturing base.
This project has shown that data-driven AI methods can accurately infer manufacturing process capabilities, enabling informed decision-making in automated process planning and supplier selection, thereby bridging the gap between design and manufacturing.
Partner With Us
Our industry partners enjoy access to our facilities for research, demonstrations, and visits, as well as a wealth of expertise from our faculty, staff, and students to discuss today’s manufacturing challenges.
For more information on partnering with GTMI, contact Belinda Vogel, our research engagement manager.